Table of Contents
What is a Water Treatment Plant (WTP)?
Water is one of the most essential elements of life, but not all water is suitable for use in homes, industries, or agriculture. In many regions, natural water contains dissolved minerals, dust, microbes, and other harmful substances. These impurities can cause damage to pipelines, reduce the efficiency of detergents, and even pose risks to human health. That is why treating water before use is extremely important.
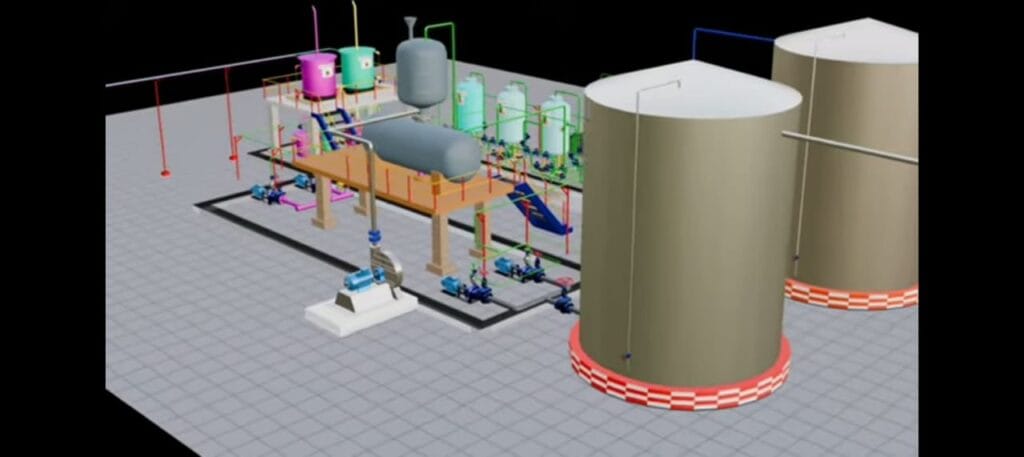
A Water Treatment Plant (WTP) is a specialized system designed to remove physical, chemical, and biological impurities from water. It converts raw, hard, and unsafe water into clean, soft, and usable water through a series of well-organized processes. WTPs are used in housing complexes, factories, hospitals, and commercial buildings to ensure that the water supplied is not only clean but also safe for drinking, bathing, cleaning, and other everyday uses.
Understanding how a WTP works gives us better awareness about how we get clean water and why it’s important to maintain such systems. In this guide, we will explore the WTP in a very simple, yet deeply informative way so even a young child can grasp the importance of water purification.
What Does a Water Treatment Plant Do?
A Water Treatment Plant (WTP) is a structured and engineered facility that transforms contaminated, hard, or impure water into clean and safe water. Its core purpose is to reduce the hardness of water and eliminate harmful substances such as dust, dissolved salts, bacteria, and other contaminants.
Hard water contains high levels of calcium and magnesium, which not only reduce the effectiveness of soaps and detergents but also lead to scaling in pipelines, boilers, and appliances. Over time, this can cause severe damage to plumbing systems and increase energy consumption. Hard water can also affect human health, particularly the skin and hair.
A WTP tackles these problems through a well-organized series of processes that involve physical filtration, chemical treatment, and sometimes biological purification. It uses a combination of tanks, filters, resins, and pumps to carefully treat the water. The goal is to make water soft, clear, odorless, tasteless, and free from dangerous elements.
Each component of the plant—from sand filters that remove suspended solids to softener tanks that inject salts and trap minerals—works with precision. Pumps distribute water from one stage to another, maintaining flow and pressure. The final product is water that meets quality standards for industrial, commercial, or household use.
So, when you turn on a tap and clean water flows out, remember that it might have travelled through a WTP where science and engineering quietly worked behind the scenes to make your water safe and gentle.
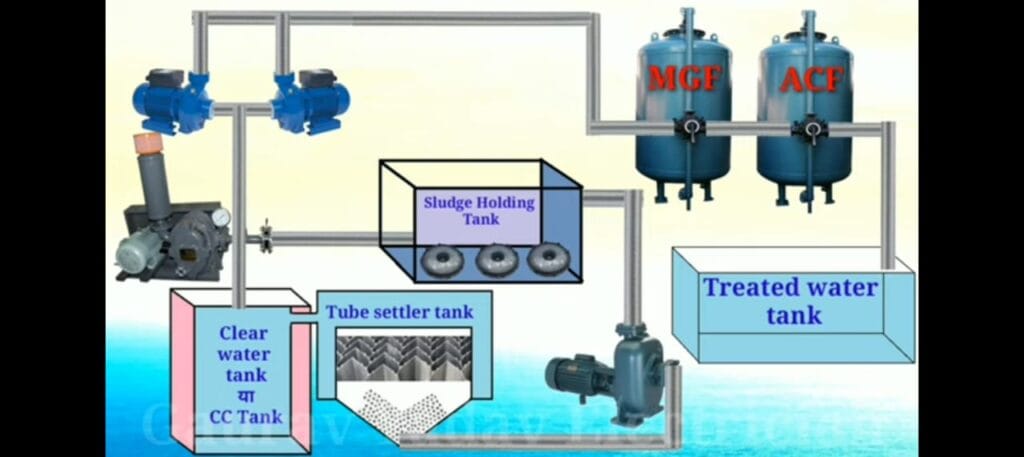
💼 Main Parts of WTP
The core of any Water Treatment Plant (WTP) revolves around two major tanks that handle both physical filtration and chemical softening of water:
- Sand Water Filter
- Softener Tank
🔧 Material Types of WTP Tanks
These tanks are built from specific materials that affect the durability, performance, and maintenance of the plant. Based on the tank material, WTPs are categorized into two types:
- M.S Plant (Mild Steel Plant): These plants use iron-based tanks that are sturdy and ideal for high-pressure environments. Mild steel tanks are typically coated internally to resist corrosion. They are suitable for large-scale industrial operations due to their strength and longevity but may require regular maintenance to prevent rust.
- F.R.P Plant (Fiber Reinforced Plastic Plant): These tanks are made from fiber material and are lighter, corrosion-resistant, and easier to install and maintain. FRP tanks are cost-effective and preferred for smaller-scale applications like residential buildings and small factories. They can withstand a wide range of chemicals and environmental conditions, making them a popular modern alternative to metal-based tanks.
Each tank type is carefully selected based on the volume of water to be treated, space availability, chemical compatibility, and operational budget. Together, these tanks form the foundation of an effective water treatment system, ensuring the right balance of purification and operational efficiency.
🭹 1. Sand Water Filter – Cleaning the Water
The Sand Water Filter is the first and most essential line of defense in the purification process. Its job is to physically separate suspended solids, organic matter, and particulate debris from raw water. This type of filter is designed to handle high volumes of water with consistent flow and pressure, ensuring smooth operation throughout the WTP.
The structure of a sand filter is composed of multiple granular layers, each having a unique particle size and function:
- Core Silex (Stones): These are the coarsest particles, located at the bottom of the filter tank. They provide foundational support and prevent finer materials above from being flushed out during backwashing. Core silex ensures stable water distribution and acts as a drainage layer.
- Fine Silex: Placed above the core layer, fine silex consists of medium-sized granules that begin the process of capturing suspended solids. This intermediate layer enhances filtration by bridging the gap between coarse gravel and fine sand.
- Sand: The topmost layer is composed of very fine grains of silica sand. This is the most active layer where the majority of filtration occurs. As water passes through this layer, tiny dust particles, algae, and organic impurities are trapped, significantly improving water clarity.
The entire setup is engineered for gravity-based filtration or pressure-based systems, depending on the plant design. Over time, as the sand filter accumulates debris, its flow efficiency reduces, which signals the need for a backwash. This cleaning cycle reverses the water flow to expel trapped waste from the filter bed.
Sand filters are vital because they reduce the load on chemical and softening units downstream. Both MS and FRP tanks use these layers, but their internal structure, volume, and pressure-handling capabilities may vary. Regular maintenance and performance checks ensure that the sand water filter continues delivering high-quality pre-treated water for the next stage.
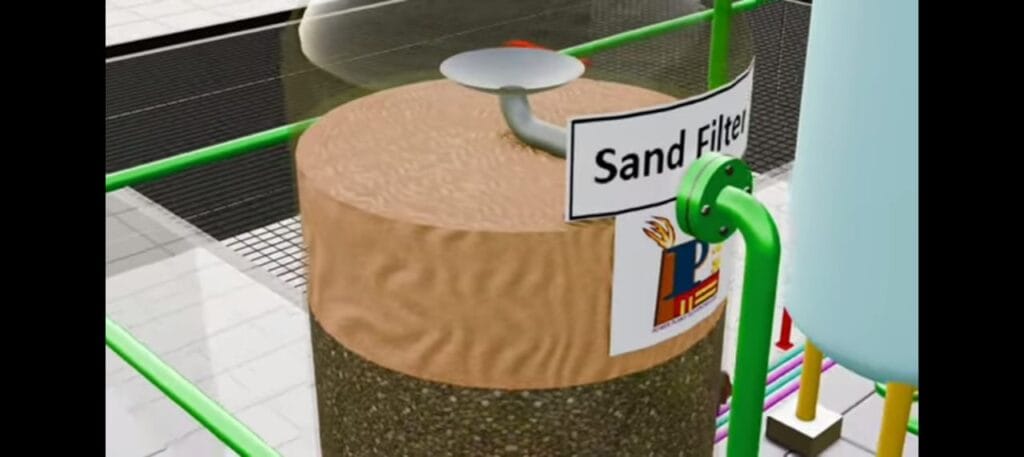
🧂 2. Softener Tank – Making Water Soft
The Softener Tank is a critical component of the water treatment process, specifically designed to reduce water hardness through ion exchange. Hard water contains high concentrations of calcium (Ca²⁺) and magnesium (Mg²⁺) ions. These minerals not only lead to scale buildup in plumbing systems and appliances but also affect the efficiency of detergents and pose skin and hair issues for users.
To combat this, the softener tank uses a process called cation exchange, which involves replacing the hardness-causing ions with sodium (Na⁺) ions. This is achieved by passing the water through a specially prepared resin bed. The resin beads inside the tank are negatively charged and are saturated with sodium ions. As hard water flows over them, calcium and magnesium ions are attracted to the resin and get exchanged with sodium.
This ion exchange process gradually saturates the resin with calcium and magnesium, reducing its efficiency. To restore the resin’s effectiveness, the system undergoes a regeneration cycle, where a highly concentrated salt solution (usually sodium chloride) is flushed through the resin. This solution displaces the accumulated hardness ions and recharges the resin with fresh sodium ions, ready for the next cycle.
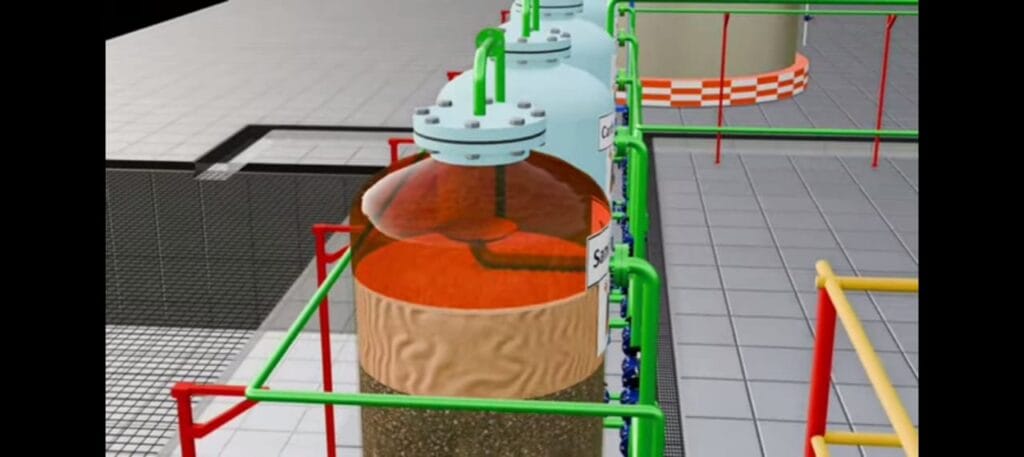
What is Hard Water?
Hard water contains high concentrations of divalent cations, primarily calcium (Ca²⁺) and magnesium (Mg²⁺). These ions are naturally picked up as groundwater passes through mineral-rich geological layers like limestone and dolomite. The hardness they cause can be:
- Temporary Hardness: Due to bicarbonates of calcium and magnesium, removable by boiling.
- Permanent Hardness: Due to chlorides, nitrates, and sulfates, which require ion exchange or chemical treatment.
Hard water forms insoluble precipitates (scales) when heated, damaging pipelines, boilers, water heaters, and reducing energy efficiency. It also prevents soap from forming lather, leading to more consumption and residue on clothes and skin.
🧬 How Does the Ion Exchange Work?
The softener tank is filled with a bed of cation exchange resin beads, which are tiny, porous spherical polymers usually made from polystyrene crosslinked with divinylbenzene (DVB). These beads contain negatively charged sulfonate groups (-SO₃⁻) that attract and hold positively charged sodium ions (Na⁺).
When hard water flows through the resin bed:
- Ca²⁺ and Mg²⁺ ions are strongly attracted to the resin beads and displace the weaker Na⁺ ions.
- Each Ca²⁺ or Mg²⁺ ion replaces two Na⁺ ions to maintain charge balance.
- The hardness ions remain attached to the resin while sodium ions enter the water.
Over time, the resin becomes saturated with Ca²⁺ and Mg²⁺, losing its effectiveness. That’s when regeneration is triggered.
🔁 Regeneration Process – Resetting the Resin
Regeneration is a multi-stage chemical reversal process that restores the resin’s sodium content:
- Brine Injection: A highly concentrated NaCl (salt) solution is pumped through the resin.
- Ion Displacement: The excess Na⁺ ions displace the Ca²⁺ and Mg²⁺ on the resin beads.
- Rinse Phase: The displaced hardness ions and residual brine are flushed out with treated water.
- Re-equilibration: The resin is now recharged with sodium ions and ready for reuse.
Important factors influencing regeneration efficiency:
- Brine concentration (typically 8–10%)
- Contact time
- Resin volume and flow rate
- Water temperature (warmer water increases exchange rate)
Key Components:
In M.S (Mild Steel) Plant:
- Core Silex: Acts as a base support layer ensuring proper water flow and distribution.
- Fine Silex: Provides intermediate support to keep the resin bed stable.
- Rexin (Ion Exchange Resin): Responsible for capturing calcium and magnesium ions.
In F.R.P (Fiber Reinforced Plastic) Plant:
- Core Silex
- Rexin (Ion Exchange Resin)
FRP designs may exclude the fine silex layer due to the internal design geometry and smaller scale of application.
Benefits of Softened Water:
- Increases the lifespan of water heaters, washing machines, and pipelines.
- Reduces soap and detergent usage.
- Leaves skin and hair feeling softer and cleaner.
- Prevents mineral buildup on bathroom fixtures and kitchenware.
This system is essential in regions with high TDS (Total Dissolved Solids) levels and is a long-term investment in water efficiency, energy savings, and user comfort. Regular maintenance of the resin and periodic regeneration are necessary to ensure consistent water softening performance.
♻️ Back Wash – Cleaning the Filter
Over time, as the sand filter continuously removes suspended solids, algae, organic matter, and fine particles from the incoming water, these impurities accumulate within the granular layers—particularly within the upper sand bed. This accumulation gradually increases resistance to water flow, reducing the filter’s efficiency and slowing down the filtration rate. If left unchecked, the filter media can become clogged, leading to higher pressure drops and reduced treatment performance.
To restore the filter’s performance, a process known as backwash is initiated. Backwashing is a critical maintenance operation in any water treatment plant. It involves reversing the direction of water flow through the sand filter to dislodge and remove the trapped contaminants. Instead of flowing from top to bottom as in normal filtration, clean water is pumped upward from the bottom of the tank, fluidizing the filter bed. The upward pressure expands the layers of core silex, fine silex, and sand, shaking loose the embedded impurities.
The dirty water is then carried away through an outlet drain, completely flushing out the accumulated waste. The process typically lasts for several minutes and continues until the outgoing water runs clear, indicating successful removal of debris. For highly loaded filters, multiple backwash cycles may be needed.
Backwashing also helps redistribute the filter media uniformly, preventing channeling and compaction which can create uneven flow paths. This process not only extends the life of the filter media but also ensures consistent water quality throughout the treatment process.
To optimize the backwashing process, some advanced systems use automatic backwash controls, pressure sensors, or timers. In manual systems, operators monitor flow rate and outlet water clarity to determine when backwashing is complete. After backwashing, the filter resumes normal operation, ready to handle the next load of raw water.
Routine and timely backwash operations are vital to maintaining the overall health, efficiency, and reliability of the Water Treatment Plant.
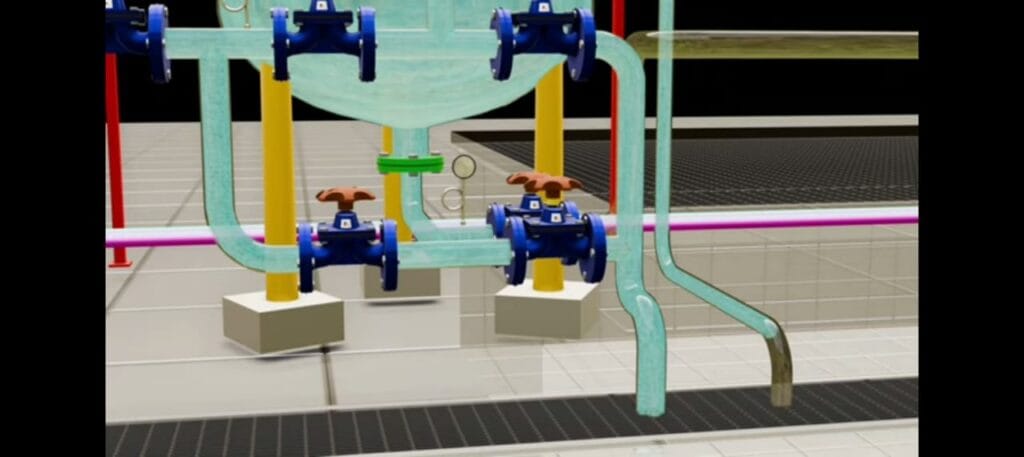
💧 Types of Pumps in a Water Treatment Plant
Inside a Water Treatment Plant (WTP), pumps serve as the driving force behind the movement and processing of water. These mechanical devices are not just used to transfer water from one chamber to another—they ensure correct flow rates, maintain required pressure levels, and support essential treatment steps like chemical dosing, filtration, and regeneration. Each type of pump plays a distinct and irreplaceable role in the efficiency and functionality of the overall plant.
Pumps in a WTP are designed based on specific criteria such as flow volume, head pressure, fluid type (raw, treated, chemical), and control systems (manual or automated). These pumps work under varied operating conditions and are often controlled by electrical panels with sensors and automatic timers for optimized performance and energy efficiency.
Here are the five key types of pumps used in a standard WTP, along with their specialized functions and technical importance:
1. Raw Water Pump
The Raw Water Pump is the first active mechanical element in the water treatment cycle. It is responsible for lifting and transferring untreated (raw) water from the source—such as a borewell, river, lake, or storage reservoir—into the raw water tank of the plant.
This pump must be capable of handling large volumes of water and dealing with varying quality and pressure. Depending on the source, the pump may have to lift water from considerable depths or draw it through long pipelines. Therefore, centrifugal or submersible pumps are commonly used, depending on whether the water is above ground or underground.
🔍 Key Functions:
- Priming and suction: It creates negative pressure to draw water up from its source.
- Flow and head control: It maintains a continuous flow and desired pressure to ensure the tank fills efficiently without overflow or cavitation.
- Contaminant tolerance: It can handle water that may contain silt, algae, or debris, especially if pre-filtration is not applied at the source.
The pump is often connected to an electric control panel equipped with timers, flow meters, or level sensors. These systems can automate the pump operation to avoid dry running (which damages the pump) or overfilling the tank.
A reliable raw water pump ensures that the entire plant has a steady and sufficient supply of incoming water, which is essential for maintaining flow balance through all treatment stages.
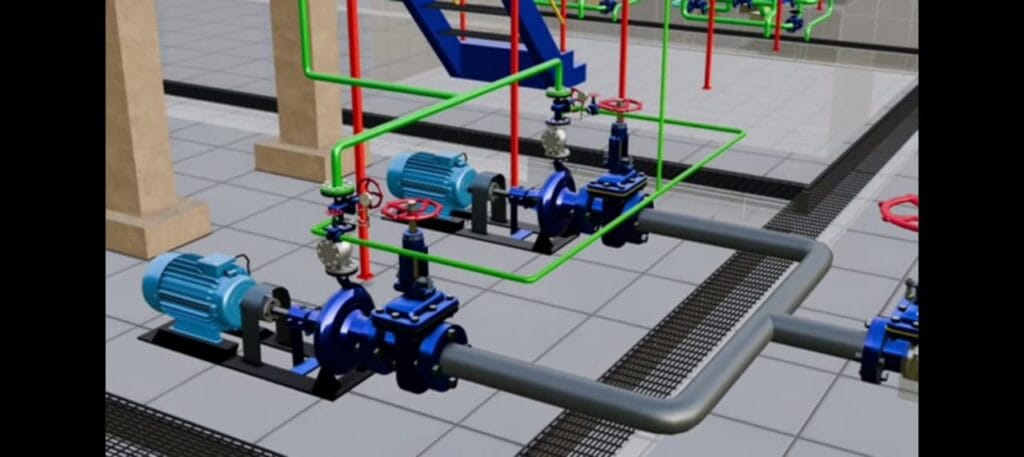
2. Treated Water Pump
The Treated Water Pump plays a crucial role in maintaining the flow of clean, softened water through the Water Treatment Plant and beyond. After the raw water has passed through the sand filter and the softener tank, this pump is responsible for transporting the now purified, softened water into the treated water tank. From there, it ensures the smooth delivery of this high-quality water to various end-use points—such as storage tanks, distribution pipelines, or point-of-use equipment.
This pump is typically a centrifugal or multistage booster pump, capable of handling moderate to high flow rates while maintaining steady pressure. It ensures the treated water reaches its destination without delay or loss in quality. Its build quality must support chemically softened water and must resist corrosion due to residual salts.
⚙️ Key Features and Functions:
- Transfer Efficiency: Moves large volumes of soft water swiftly to the treated water tank.
- Pressure Management: Maintains consistent water pressure to support further pumping stages, like hydropneumatic systems.
- Material Compatibility: Constructed with corrosion-resistant materials (such as stainless steel or anti-scale coatings) to handle soft water efficiently.
- Automation-Ready: Often integrated with float switches or level sensors in the treated water tank to start and stop the pump automatically, avoiding dry runs or overflows.
The treated water pump ensures that the high-quality water prepared by the WTP does not go to waste and reaches where it is needed—whether for drinking, industrial processes, bathing, or other uses. A dependable treated water pump enhances the WTP’s efficiency and reliability by making sure the clean water gets delivered precisely, safely, and without interruption.
3. Hydropneumatic Pump
The Hydropneumatic Pump is a specialized pressure-boosting system that plays a key role in delivering water to end users with stable and consistent pressure. It works in coordination with an air pressure tank, which contains both water and compressed air. The unique interaction between these two elements enables the system to push water with force even when the primary pumping system is turned off.
Here’s how it works in detail:
- After water is treated and stored in the treated water tank, the hydropneumatic pump draws this water and pumps it into an airtight pressure vessel. Inside this tank, air is compressed on top of the water, creating stored energy in the form of pressure.
- When a user opens a tap or a shower, the compressed air pushes the water out instantly, giving strong, pressurized flow without the pump needing to run every time. This not only saves energy but also reduces the wear and tear on the pump.
- The pump is fitted with a smart component called an NRV (Non-Return Valve), which ensures that once the water moves forward, it doesn’t flow backward into the system. This protects the pump and maintains pressure integrity within the system.
- A pressure switch is also connected to monitor tank pressure. When the pressure drops below a set point (due to water usage), the pump automatically turns on to recharge the tank with water. Once the required pressure is reached again, it switches off.
🔧 Benefits of a Hydropneumatic Pump System:
- Constant Water Pressure: Delivers stable water pressure across multiple floors and taps, especially useful in multi-storey buildings.
- Energy Efficient: Reduces frequent motor starts by using stored pressure.
- Compact Design: Requires less space and works silently.
- Longer Life for Pump: Minimizes on/off cycles, thus increasing pump durability.
This system is ideal for homes, commercial complexes, hotels, and hospitals where consistent water pressure is critical. It ensures that whether you’re taking a shower on the top floor or filling a washing machine on the ground floor, the pressure remains strong and steady throughout the day.
4. Dozing Pump
The Dozing Pump is a precision device used to inject a controlled amount of chlorine or other disinfectants into the treated water. This stage is essential for microbial disinfection, ensuring the final water output is free from harmful bacteria, viruses, and other pathogens.
🔬 Purpose:
- After water passes through the softener tank, it may still contain microbiological contaminants invisible to the eye. Even softened water can harbor bacteria, which may grow rapidly in pipelines and storage tanks. To ensure complete safety, chlorination is necessary.
⚙️ Working Principle:
- The pump is usually a diaphragm or peristaltic type, engineered for chemical compatibility and precise dosing.
- It draws liquid chlorine (typically in the form of sodium hypochlorite) from a storage tank.
- A flow controller or PLC (Programmable Logic Controller) adjusts the chlorine quantity based on water flow rate or required parts-per-million (ppm) concentration.
- As water flows out of the softener, the dozing pump injects the chlorine in real-time, ensuring uniform disinfection.
🧪 Safety and Monitoring:
- Excess chlorine can cause taste and odor issues, while too little fails to disinfect. So, it is important to monitor chlorine residual levels using test kits or automated sensors.
- In advanced systems, the dosing process is synchronized with online analyzers and feedback loops to adjust dosing dynamically.
✅ Benefits:
- Ensures water is biologically safe for human use.
- Prevents growth of biofilms in pipelines and tanks.
- Reduces risk of waterborne diseases.
This pump is strategically installed after the softener tank, as softened water improves chlorine efficiency by reducing competing ions like calcium and magnesium that may otherwise interfere with the disinfection process.
5. Dewater Pump
- It removes the wastewater that collects in the tanks during salt injection and backwash.
- This keeps the system clean and efficient.
Advanced Insights: Deep Technical Knowledge of Water Treatment Plants
To enhance your blog post, we can include the following expert-level topics:
1. Detailed Chemical Reactions in the Softener Resin
Explore how the cation-exchange resin works at a molecular level:
- Reaction Example: Ca2++2Na-R→Ca-R2+2Na+
- where R = resin functional group (usually sulfonated polystyrene).
- Explain how selectivity coefficients govern resin efficiency.
- Talk about how resin fouling occurs due to iron, manganese, or organic matter.
2. Water Quality Standards (IS 10500, WHO, BIS)
Introduce Indian and global standards for treated water:
- BIS IS:10500 (2012) for drinking water
- Acceptable vs permissible limits for hardness, TDS, chlorine, turbidity
- Explain test procedures for verifying water quality: EDTA titration for hardness, turbidity meters, etc.
3. Design Parameters of Sand Filters
- Filtration velocity: 5–15 m³/m²/h (varies by pressure vs gravity filters)
- Effective size of sand: 0.45–0.7 mm, Uniformity Coefficient (UC) ≤ 1.7
- Backwash rate: 15–30 m³/m²/h
- Hydraulic loading rate and bed expansion percentage during backwash
- Discuss breakthrough curves and filter run time
4. Pump Head Loss Calculations
- Total Dynamic Head (TDH) = Static Head + Friction Loss + Minor Losses
- Use Darcy-Weisbach or Hazen-Williams equation for pipe losses
- Emphasize the role of NPSH (Net Positive Suction Head) and pump curves
5. Softener System Sizing and Salt Dosage
- How to size a softener based on hardness and flow rate: Resin Volume (L)=Daily Hardness Load (g)×1000Exchange Capacity (g/L)
- Typical resin capacity: ~40,000–50,000 grains/ft³ (~1000–1200 g/L)
- Salt dose per regeneration: 100–150 grams per liter of resin
- Regeneration frequency and control valve types (time-based vs volume-based)
6. Automation and SCADA Integration
- Overview of Programmable Logic Controllers (PLCs) and SCADA systems for:
- Remote monitoring of flow, pressure, chlorine levels
- Alarm triggers for low/high tank levels
- Regeneration cycles and chemical dosing feedback loops
- Benefits: Reduced manpower, better quality control, data logging
7. Membrane Technologies (Optional Add-on for Advanced WTPs)
- Add-on options like Ultra Filtration (UF) or Reverse Osmosis (RO):
- RO membrane pore size ~0.0001 microns
- Rejects TDS, heavy metals, pesticides, etc.
- Pre-treatment importance before RO (SDI ≤ 5, no chlorine)
8. Resin and Media Lifespan + Disposal
- Resin lifespan: 5–10 years (depends on iron content, regeneration frequency)
- Sand media: ~3–5 years
- Media exhaustion signs: increased hardness in output, flow drop, high ΔP
- Disposal practices as per Hazardous Waste Management Rules in India
Environmental Impact – Sustainability in Water Treatment
A responsible WTP must minimize its ecological footprint:
🌱 Challenges:
- Salt waste from regeneration is highly saline and needs careful disposal.
- Backwash water is rich in suspended solids—requires settling tanks or sludge handling units.
- Excess chlorine, if discharged, damages aquatic ecosystems.
✅ Eco-Friendly Solutions:
- Zero Liquid Discharge (ZLD) systems reuse every drop.
- Brine Recovery Units reclaim salt from wastewater.
- Solar-Powered Pumps lower carbon emissions.
- Biological Filters can replace sand in some systems.
Would you like me to continue with topics like:
- Detailed Electrical Control Panel Design for WTPs
- How to Size a WTP for a Building or Industry
- Daily, Weekly & Monthly Maintenance Schedules
- Troubleshooting Guide for Common WTP Problems
FAQ
What is a Water Treatment Plant (WTP)?
A Water Treatment Plant is a facility that cleans dirty or polluted water and makes it safe for drinking, cooking, and other uses. It removes harmful substances like bacteria, chemicals, dirt, and waste.How does a Water Treatment Plant work?
A WTP works through several steps:
Screening: Removes big objects like leaves and plastic.
Coagulation & Flocculation: Adds chemicals to group tiny particles into larger clumps.
Sedimentation: These clumps settle at the bottom.
Filtration: The water passes through filters to remove remaining dirt.
Disinfection: Chemicals like chlorine or UV light kill germs and viruses.
The final water is then clean and safe for use.Are there any disadvantages of a WTP?
High cost of setup and maintenance
Energy consumption
Sludge disposal issues
However, the benefits are much greater than these drawbacks.What are the advantages of a Water Treatment Plant?
Safe drinking water
Improved public health
Recycling and reuse of water
Support for agriculture and industries
Reduced pollution in rivers and lakes