Table of Contents
key phase
Transformers work on the principle of mutual induction. They have primary and
secondary windings that are electrically isolated from each other. As these windings
are wound on the same magnetic core, they are magnetically coupled to each other.
The magnetic core is made from the laminations of either CRGO silicon steel or the
amorphous alloy.
The winding to which input ac source is connected is called as ‘Primary winding’ and
that across which the electrical load is connected is called as ‘Secondary winding’. Any
winding of a given transformer can be used as primary and secondary.
Transformers transform electrical potential from one level to another at same
frequency. In other words, frequency remains same on both sides.
Power (watts) and volt-amperes in an ideal transformer remains same on both sides.
In an ideal transformer, No-load current is used only for magnetizing the core.
Therefore in an ideal transformer, Io = Iµ and Iw = 0.
Two types of power loss takes place in a transformer. (i) Iron loss takes place in the
magnetic core and (ii) Copper loss takes place in the copper windings.
Iron loss remains constant for all values of load (from No-load to Full-load) provided
that the input voltage and input frequency supplied to the transformer are not changed.
Hence, iron loss is also called as ‘No-load loss’ and ‘Constant loss’.
Copper loss varies as square of currents which in turn varies with changes in load.
Hence, it is also called as ‘Variable loss’.
Iron loss comprises of (i) Hysteresis loss and (ii) Eddy current loss.
Being a static device, mechanical loss (i.e. friction and windage) is absent in
transformers hence, its efficiency is always greater (> 90%) than the efficiency of
rotating machines.
To reduce the hysteresis loss, core laminations are made from highly permeable
material like CRGO silicon steel or amorphous alloy.
To reduce the eddy current loss, the magnetic core is made from a stack of thin
laminations which are insulated from each other before forming the stack.
INTRODUCTION
Electrical energy is particularly useful because it can be transferred over long distances and distributed
in a wider network and converted into other desired forms efficiently and economically. All this have
become possible mostly due to the availability of a static electromagnetic device called as Transformer.
It is a simple device which interlinks two or more electrical circuits by a common magnetic circuit.
There are no moving parts. Transformers can increase or decrease the voltage or current in an ac circuit.
They can electrically isolate different ac circuits from each other.
. In power system, it is said that in the
entire world, after electricity is produced in power stations, it is transformed into different voltage levels
three to four times before it finally reaches the consumer end. Fig. 3.1 shows a schematic of how transfer
of electric power takes place from generating station to the user.
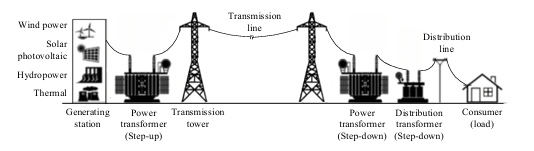
Transformers work on the basic principle of mutual induction. It is known that, the flow of current
in any circuit (or a conductor) is always associated with magnetic field surrounding that conductor. If
the current is of alternating type then its magnetic field will also change in magnitude and direction in
accordance with the changes in current with respect to time.
This is the reason why we say that the
magnetic flux produced by a current is in phase with that current. Now, if another circuit is placed in
the vicinity of the first circuit which is carrying alternating current than, the second circuit will link with
some of the alternating flux produced by first circuit and therefore an emf will be induced in the second
circuit. This is called mutual induction. Because, it works on the principle of mutual induction,
transformers are operated on ac supply and not on dc. As there are no moving parts, the power loss due
to mechanical friction and windage is zero and little maintenance is required as compared to rotating
machines. This results in high efficiency of transformers which lie between 94% – 96% approximately.
TRANSFORMER AND ITS TYPES
Transformer is a static electromagnetic device which transforms electrical potential from one level to
another by mutual induction at same frequency on both sides i.e. input and output sides. It is mostly
used in power system networks to step-up or step-down the voltage. Hence, the voltage levels on the
two sides may or may not be equal depending upon for what application it is designed and fabricated.
In electronic circuits, it is used to match the source and load impedances for maximum power transfer
between them. It should be understood that, transformer is not an energy conversion device but a device
that transforms electrical energy at same or different voltage and current levels. The size of transformer
varies from very small ones that are used in audio, video and communication related electronic circuits
to power transformers of thousands of MVA rating used in power system. Transformers can be
classified on the basis of many aspects as shown in Fig. 3.2. In spite of these variations, all transformers
work on the same principle and also, their basic philosophy of construction remains same.
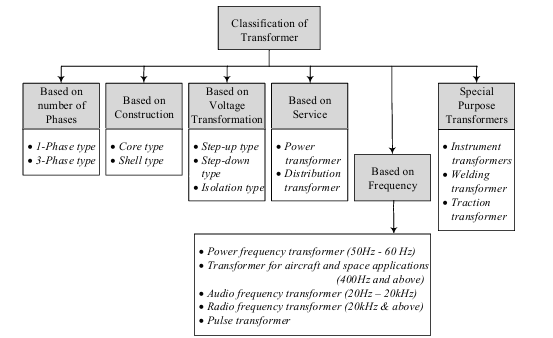
In its simplest form, transformer consists of a magnetic core on which windings are wound. A single
phase transformer has minimum two windings, one for the input side and one for the output side. A
three-phase transformer has minimum six windings, three on each side which are either connected in
star or delta configuration. The winding across which input ac source is connected is termed as Primary
winding whereas the winding across which electrical load is connected is called as Secondary winding.
The current in primary winding produces an alternating magnetic flux that travels through the core and
links with the secondary winding where it induces emf by mutual induction.
Similarly, the current in
secondary winding establishes its own flux which links with primary winding. For a given transformer,
though any side can be used as primary and secondary, care should be taken to limit the input voltage
within the permitted voltage rating of the winding. Single phase transformers are normally used in
electronic circuits, control circuits and domestic equipment. The three-phase transformers are employed
in power system.
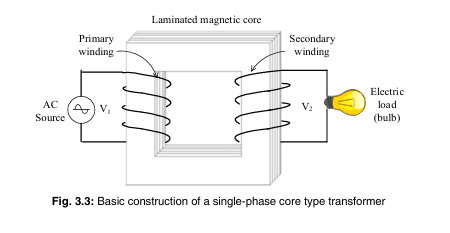
CONSTRUCTION OF 1-PHASE TRANSFORMERS
The conventional transformers has following main elements:
(a) A magnetic circuit (core) comprising of limbs and yokes and
(b) Two electric circuits comprising of primary winding and secondary winding.
Based on the shape of magnetic core, transformers is classified as (a) Core type and (b) Shell type. The
horizontal sections of magnetic core are called as Yoke and the vertical ones are called as Limb. In
single-phase transformer, the core type construction has two limbs and the windings are wound on both the limbs. Shell type construction has three limbs and both windings, primary and secondary are wound
on middle limb only
Construction of Magnetic Core
When the transformer is in operation, some amount of active power (watts) is lost in the magnetic core
as well as in the windings. This power loss produces heat which gets dissipated to the surrounding area.
Like any other electrical equipment, insulating items like electrical grade insulating paper, Bakelite
sheet, pressboard, wood etc. are used in a transformer. Production of heat due to power loss imposes
risk to these insulations. Therefore, all efforts are made during the manufacturing stage to ensure the
power loss at minimum value. The power loss in magnetic core is called as core loss, iron loss or No
load loss. This core loss is further divided into two types as (a) hysteresis loss and (b) eddy current loss.
Different aspects related to the construction of core are based on the minimization of this core loss.
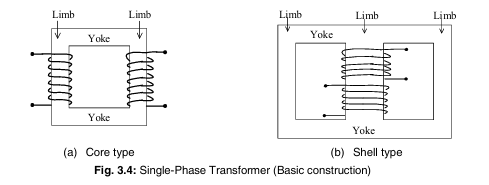
Use of silicon-steel alloy for reduction of hysteresis loss
(A)
Use of silicon-steel alloy for reduction of hysteresis loss
Hysteresis loss (Ph) is produced due to continuous reversal in the direction of magnetization of the core
because, the magnetic flux established in the core is of alternating type. To minimize hysteresis loss,
the magnetic core should be made from a material that has high permeability. Commonly used material
are CRGO silicon-steel alloy and amorphous alloy. Addition of silicon in iron increases its permeability.
Addition of silicon content also increases the material resistivity which consequently helps in the
reduction of eddy currents. A small amount of silicon (about 3%) is added in iron to produce the silicon
steel alloy. Higher content of silicon in iron tends to make the material brittle and difficult to cut in
required shape for making the stampings. Different types of material used for magnetic core are dealt
in detail in the section.
Use of laminated core for reduction of eddy current loss
Eddy current loss results from the induction of eddy currents in the core when it carries alternating flux.
These eddy currents whirl round and round in the form of concentric circles. This phenomenon can be
visualized as identical to the eddies developed in water bodies. In order to minimize the power loss
produced by eddy currents, the magnitude of eddy currents should be minimized by reducing the area
of cross-section of the path where eddy currents are produced. For this purpose, the core is made from
several pieces of thin sheets of silicon-steel instead of making it a solid one-piece core. The resulting
core is called as laminated core and the thin sheets are called as lamination or stamping. Their thickness
varies between 0.3 and 0.5 mm. To make a transformer core, first a thin coat of heat resistant enamel
insulation like varnish, is applied on all sides of every stamping. Thereafter, they are stacked over each
other and then tightly clamped together to form a solid core structure. As a result, eddy currents from
one stamping cannot enter into the adjacent stamping and the sum total of eddy currents produced in all
stampings is much less than the eddy current that would have been produced in a non-laminated core.
Thus a laminated core results in reduced eddy current loss.
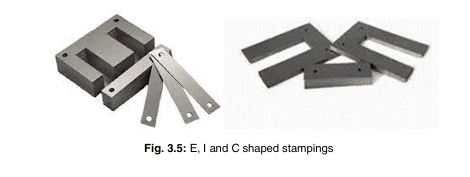
Core cross-section and interleaving of joints
For single phase transformer, stampings are available in their standard shapes identical to the
English letters ‘L, I, C and E’. These individual pieces are joined together to form the core. To reduce
the reluctance offered by magnetic core to the flux established in it, continuous joints in the core cross
section should be avoided so that there is no continuous air gap in the path of magnetic flux. This is
ensured by interleaving the joints in adjacent layers of stampings. This is shown in Fig. 3.6(a). There
are different methods of interleaving by adopting different types of joints. Butt joints as shown in Fig.
3.6(b) are suitable if Hot Rolled Steel (H.R.S.) is used for making the stampings. But for the Cold Rolled
Grain Oriented steel (CRGO), such joints are not suitable. This is because at the place of joints, the flux
path becomes at right angle to the direction of rolling which increases the magnetization current and
power loss in the core. Therefore, for CRGO, mitred joints are used for interleaving as shown in Fig.
3.6(c). More information of CRGO and rolling process is provided in Section
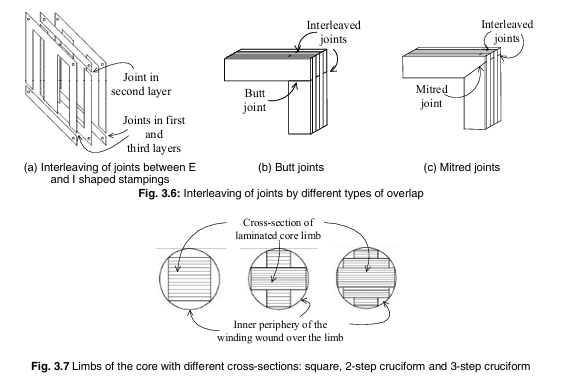
Single-Phase Core Type Transformer
Single-phase core type transformer has a magnetic core with two limbs. Two windings of concentric
type also called as cylindrical type are wound spirally over the limbs. In the basic construction of core
type transformer presented in Fig. 3.3, it was shown that, all the turns of primary winding are wound on
one limb and all turns of secondary winding are wound on the second limb. This type of construction
assumes that, all the flux produced by each winding will travel through the core and link with the second
winding. Practically, some part of the total flux produced by each winding completes its path through
air without travelling in the core and therefore, does not link with the other winding. This part of each
flux which does not link with the other winding is called as leakage flux and it serves no useful work.
Hence, if the two windings are wound away from each other on different limbs, they are not able to use
all the flux established by each other. To minimize the effective leakage flux, both windings of a core
type transformer are halved and wound on both limbs one over the other with an insulating paper
maintained between them.
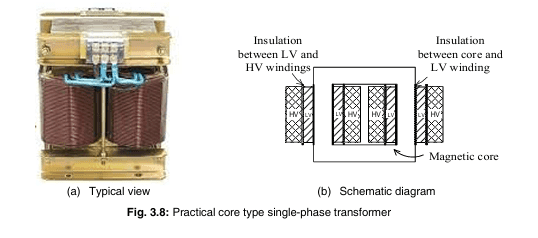
For step-up and step-down applications, the two windings are designed for different voltage ratings.
One of them is a high voltage (HV) winding while the other one is the low voltage (LV) winding. The
LV winding is wound on the inner side and the HV winding is wound on the outer side. This is primarily
done to reduce the cost of insulation and to ease the provision of tappings. In case of On-load tap
changing, tappings are provided on the HV winding. The thickness of insulating material that is
provided between the core and inner winding as well as between the two windings which are wound
one over the other depends upon the potential difference that will appear across the insulation.
Single-Phase Shell Type Transformer
In shell type transformer, the LV and HV windings are wound over the central limb. These windings
are of sandwich type as shown in Fig. 3.9(b). Each winding is subdivided into subsections. LV and HV
subsections are alternately put in the form of sandwich. Since the core is grounded, LV winding is
placed closer to the core so that the cost of insulation between the core and the winding closer to it is
less. Note that, the bottom and top LV coils are of half the size of other LV coils.
Since both windings are on the central limb, it has total flux produced by both windings which then gets
divided equally and returns back through the outer two limbs. Due to this reason, the area of cross
section of middle limb is twice that of the two outer limbs. As both windings are able to link with almost
all the flux produced by each other, the leakage flux is less and hence the leakage reactance is also less.
This results in better voltage regulation.
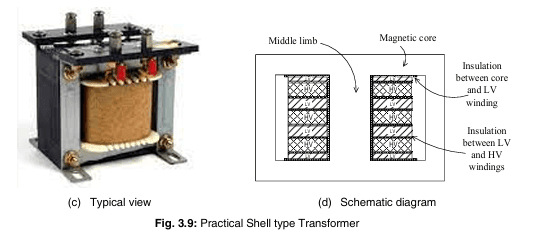
Differences Between Core Type and Shell Type Transformers
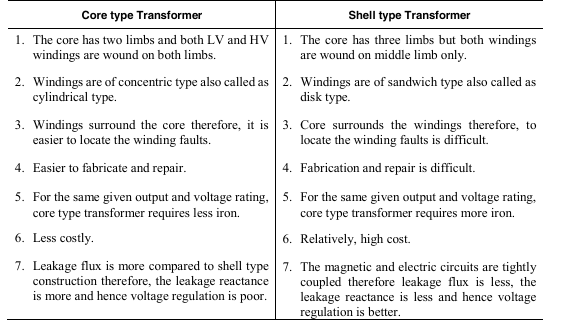
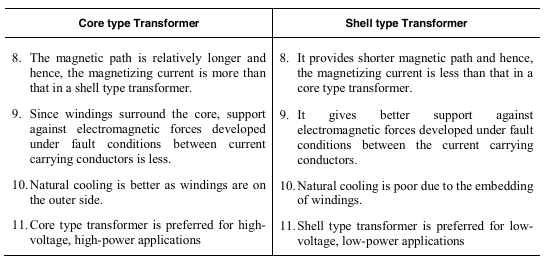
Hot Rolled Steel
In the hot rolling process, a large rectangular slab of metal or alloy referred to as a billet (which is to be
processed) is heated above its recrystallization temperature (usually 1700° F or greater) and then
compressed into a large roll of thin sheet. While still hot, it is passed through a series of rotating rollers
to achieve the required dimensions and then allowed to cool. During the process of hot rolling at
temperature higher than the recrystallization temperature of the material, the crystals (grains) get
damaged and the temperature does not allow ‘recrystallization’. Recrystallization is a process where the
damaged grains are replaced with a new set of grains during the rolling process. This can happen only
when the metal is cool, so any metalworking process that involves forming the metal at temperatures
above the recrystallization point is considered as “hot rolled”.
2 Cold Rolled Non-Grain-Oriented Steel (CRNGO)
Cold rolled steel is the hot rolled steel that has undergone additional processing to improve its
dimensional and mechanical properties. During the cold rolling process, cooled hot rolled steel passes
through another series of pairs of rollers at room temperature. Since the material is no longer hot and
malleable, a significantly higher amount of pressure is required to compress it into the desired shape.
While this process is more labour-intensive and costlier than the hot rolling process, it can achieve
tighter dimensional tolerances and better surface qualities. Cold rolled has about 20% more physical
strength than that of hot rolled steel. This makes it more suitable for use in high-stress applications.
A cold rolled non-grain-oriented-steel, usually has silicon content of 2 to 3.5% and has similar
magnetic properties in all directions. In other words, it is isotropic in nature. CRNGO is less expensive
than CRGO. It is used when cost is more important than efficiency and is preferred in applications
where the direction of magnetic flux is not constant. Example, stator and rotor cores of rotating
equipment like electric motors and generators. This is because, in rotating machines, the cross section
is circular and hence the magnetic field at each point is tangential to circle. It means that the magnetic
field changes its direction at every point.
Cold Rolled Grain-Oriented Steel (CRGO)
In cold rolled grain oriented steel, the silicon content is usually about 3%. By fully annealing during the
cold rolling process, the grains are oriented in the direction of rolling. Consequently, the permeability
is high and magnetic flux density is increased by 30% only in the direction of rolling compared to other
directions. Thus CRGO is magnetically superior in the rolling direction. If the magnetic flux is oriented
in the direction of rolling then it experiences less reluctance and hence the core loss is less. This alloy
is commonly used for the cores of power and distribution transformers. CRGO is usually supplied by
the steel mills in the form of roll or coil. It has to be shear cut into laminations of required size and
shape to use them for transformer core.
Amorphous Core
The core of the first practical transformer was made from carbon steel sheets by William Stanley in the
year 1885. It was then replaced by Silicon-steel alloy in order to reduce the core losses. While CRGO
silicon-steel is commonly used for the transformer core, introduction of amorphous alloy core is also
receiving increasing popularity.
Amorphous core transformer is a kind of energy efficient transformer in which the core is made
from very thin foils of amorphous alloy composed of about 80% iron and remaining about 20% is a
mixture of boron and silicon. The amorphous alloy is a soft ferromagnetic material. It is formed by a
process of rapid solidification of molten alloy. Due to high speed of solidification, the atoms get no
opportunity to form crystalline structures (grains) and they solidify in a disordered manner (i.e.
amorphous). This allows it to be magnetized and de-magnetized quickly in any direction with very less
core loss. In other words, it is isotropic. Due to the non-crystalline structure, it has higher electrical
resistivity which is about three times compared to the typical silicon-steel lamination sheets. Also, the
thickness of amorphous foil is very less (about 0.025 mm). High resistivity and very less thickness of
the foil results in significant reduction in eddy current loss [11]. Consequently, the core loss in
amorphous core transformer is about one-third of that in conventional CRGO core transformer.

PRINCIPLE OF OPERATION
Consider a two-winding transformer with secondary winding open
(not connected to load) as shown in Fig. 3.12. This is called as no
load condition. When an ac voltage V1 is applied across the
primary winding, some current starts flowing through it. This
current is called as No-load current and is denoted by Io. It sets up
an alternating magnetic flux ∅ in the core which links with both
the windings. By Faraday’s law of electromagnetic induction, due
to flux-linkage of this flux ∅ with the windings, it induces emf in
both windings. Their RMS values are denoted by E1 and E2 for the
primary and secondary windings respectively. E1 is called, the self
induced emf and E2 is called the mutually-induced emf. The self
induced emf E1 opposes the applied voltage V1 due to Lenz’s law.
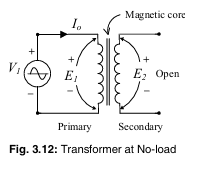
Now, if the secondary winding circuit is closed by connecting an
electrical load across it than, the emf E2 will drive a current I2 in the secondary winding and in the load.
Thus ac power from primary circuit is transformed to the secondary circuit by mutual induction. The
polarities shown in Fig. 3.12 are the instantaneous polarities of ac voltages and emfs.
CONCEPT OF IDEAL AND PRACTICAL TRANSFORMERS
It is known that, ideal systems are those which have no losses. The output power delivered by them is
equal to the input power drawn by them from the source and therefore, their efficiency is 100%.
Practically, ideal systems do not exist but all practical systems should be designed to perform close to
their ideal counterparts. An ideal transformer is considered to have the following properties:
The resistances R1 and R2 of primary and secondary windings are zero. Therefore, the
respective voltage drops (I1R1 and I2R2) and the copper losses are also zero.
The complete magnetic flux produced by each winding travels through the magnetic core and
links with the other winding. In other words, the leakage flux is zero.
Permeability of the magnetic core is constant i.e., the core always remains in unsaturated state.
At No-load condition when the secondary winding is open, the No-load current Io flowing in
primary winding is utilized for the production of magnetic flux only. In other words, the No
load current Io is a purely magnetizing (i.e. purely inductive) current and lags the applied
voltage V1 by 90o. Hence, the input power taken by an ideal transformer at No-load condition
from the source is
= cos90 =0.
Both, iron loss and copper loss in an ideal transformer are zero at No-load as well as at On
load conditions. Therefore, the efficiency is always 100%.
LOSSES AND EFFICIENCY
In a practical transformer, a certain fraction of input power is wasted in the form of heat and
consequently, the output power of the transformer is less than its input power. This power loss is a loss
of active power and can be classified in two categories (i) Iron-loss (Pi) and (ii) Copper-loss (Pcu). As
the names imply, iron-loss takes place in the magnetic core and therefore is also called as Core Loss or
No-load loss or Open-circuit loss. The copper loss takes place in primary and secondary windings that
are made from copper and is also called as Ohmic loss.
Total loss in a transformer = Iron loss (Pi) + Copper loss (Pcu)
Iron Loss
In Section 3.3.1, it was informed that the iron-loss is of two types, (i) Hysteresis loss (Ph) and (ii) Eddy
current loss (Pe). Hysteresis loss is produced because the magnetic core is continuously subjected to
reversal of magnetization by the alternating magnetic flux ∅. And to minimize this loss, it is necessary
that a highly permeable material like CRGO silicon-steel alloy or amorphous alloy should be used to
fabricate the core laminations. More details about these alloys are given in Section
Eddy current loss is produced due to the induction of eddy currents in the core by alternating
magnetic flux. To minimize this loss, the core is made from thin insulated stampings or laminations and
such a core is said to be a laminated core. For more details, revisit Section
Iron loss (Pi) = Hysteresis loss (Ph) + Eddy current loss (Pe)
Copper Loss
The loss of active power that takes place in copper windings is called as copper loss. It is due to the
ohmic resistances (R1 and R2) of the two windings. The total copper loss in a transformer is given by,
From above equations, it is clear that the copper loss varies as square of current. Since the winding
currents are directly proportional to load, it means that copper loss will vary with any changes in the
magnitude of load. Hence it is also called as Variable loss.
Efficiency
Efficiency of a transformer is defined as the ratio of active output power to active input power. Hence,
it is also referred as Power efficiency or Commercial efficiency. Since efficiency is based on active
power (in watts) and not on the apparent power (in volt-amperes), it depends on power-factor (cos∅).
For a given volt-ampere load, efficiency is highest at unity power-factor.
fAQ
what is a transformer?
Transformers work on the principle of mutual induction. They have primary and
secondary windings that are electrically isolated from each other. As these windings
are wound on the same magnetic core, they are magnetically coupled to each other.