Introduction to Single-Phase Transformers
A single-phase transformer is a fundamental electrical device that transfers electrical energy between circuits through electromagnetic induction. It is widely used in power distribution, voltage regulation, and isolation applications. Unlike three-phase transformers, which handle balanced loads in industrial settings, single-phase transformers are common in residential and small-scale commercial systems.
An electrical power transformer is a static device that transforms electrical energy from one circuit to another
without any direct electrical connection and with the help of mutual induction between two windings. It
transforms power from one circuit to another without changing its frequency, but may be at a different voltage level.
A single-phase transformer is a type of power transformer that utilizes single-phase alternating current, meaning
the transformer relies on a voltage cycle that operates in a unified time phase.
The working principle of the single-phase transformer is based on Faraday’s law of electromagnetic induction.
Basically, mutual induction between two or more windings is responsible for the transformation action in an electrical
transformer
Why Are Single-Phase Transformers Important?
Single-phase transformers play a crucial role in:
Stepping up the voltage for efficient power transmission
Stepping down the voltage for safe household use
Providing electrical isolation in sensitive equipment
Enabling voltage conversion in electronic devices
Construction of a Single-Phase Transformer
The construction of a single-phase transformer involves carefully designed components that work together to enable efficient voltage transformation. Each element plays a critical role in the transformer’s performance, efficiency, and durability. Below is a detailed breakdown of the key components and their characteristics.
Core Assembly
The transformer core serves as the magnetic pathway for flux linkage between windings. Modern transformers use laminated silicon steel cores to minimize eddy current losses. The laminations are insulated from each other with a thin varnish coating, typically 0.3-0.5mm thick, which significantly reduces circulating currents while maintaining high magnetic permeability.
Winding Configuration
Single-Phase Transformer windings consist of precisely wound copper or aluminum conductors arranged concentrically around the core. High-voltage windings use finer gauge wire with more turns, while low-voltage windings employ thicker conductors. The winding process requires careful layer insulation using materials like kraft paper or Nomex to prevent inter-turn shorts and withstand operational voltages.
Insulation System
A multi-layer insulation approach protects the transformer from electrical breakdown. Major insulation components include:
Conductor insulation (enamel or paper wrap)
Layer insulation between winding sections
Main insulation between windings and core
Barrier insulation between primary and secondary windings
Core Materials and Design
The primary winding is supplied with an alternating electrical source. The alternating current through the primary
winding produces an alternating flux that surrounds the winding. Another winding, also known as the secondary
winding, is brought close to the primary winding. Eventually, some portion of the flux in the primary will link
with the secondary. As this flux is continually changing in amplitude and direction, there is a change in flux
linkage in the second winding as well. According to Faraday’s law of electromagnetic induction, an electromotive
force (emf) is induced in the secondary winding, which is called as induced emf. If the circuit of the secondary
winding is closed, an induced current will flow through it. This is the simplest form of electrical power
transformation; this is the most basic working principle of a transformer.
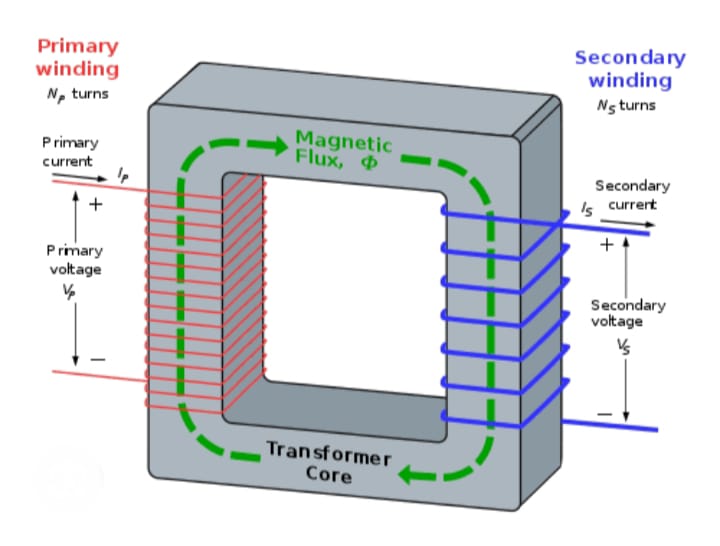
It consists of two coils of electrical wire called inner and outer windings. The primary is usually known to have
a higher amount of voltage. Both coils are wrapped around a common closed magnetic iron circuit, which is
referred to as the core. The core is made up of several layers of iron, laminated together to decrease losses. Being
linked at the common core allows power to be transferred from one coil to the other without an electrical
connection. When current passes through the primary coil, a magnetic field is created that induces a voltage in
the secondary coil. Usually, the primary coil is where the high voltage comes in and is then transformed to create
a magnetic field. The job of the secondary coil is to transform the alternating magnetic field into electric power,
supplying the required voltage output.
Insulation System
A multi-layer insulation approach ensures safety and longevity:
Insulation Type | Materials Used | Purpose |
---|---|---|
Conductor Insulation | Enamel, paper, or polymer | Prevents short circuits between turns |
Layer Insulation | Kraft paper, Nomex | Separates winding layers |
Ground Insulation | Pressboard, bakelite | Isolates windings from core |
Major Insulation | Oil-impregnated paper | Separates primary-secondary |
Working Principle of a Single-Phase Transformer
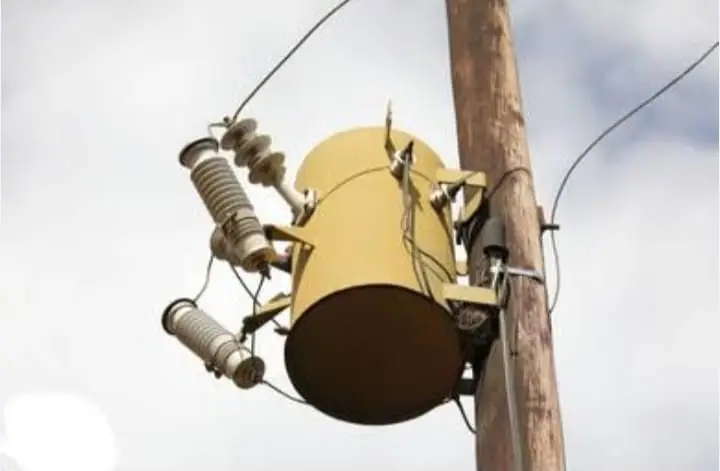
Fundamental Operating Concept
A single-phase transformer operates on the principle of electromagnetic induction, discovered by Michael Faraday in 1831. This static electrical device transfers electrical energy between two or more circuits through a shared magnetic field, without any moving parts.
Core Mechanism: Faraday’s Laws in Action
The transformer functions through two fundamental electromagnetic principles:
Faraday’s First Law of Electromagnetic Induction
When a conductor is placed in a varying magnetic field, an electromotive force (EMF) is induced
Faraday’s Second Law of Electromagnetic Induction
The magnitude of induced EMF is proportional to the rate of change of flux linkage
According to Faraday’s law,
“Rate of change of flux linkage concerning time is directly proportional to the
induced EMF in a conductor or coil”.
The principle of operation of a transformer has been explained in the following simple steps:
- As soon as the primary winding is connected to a single–phase supply, an AC starts flowing through it.
- An alternating flux is produced in the core by the AC primary current.
- The alternating flux gets linked with the secondary winding through the core.
- Now, according to Faraday’s laws of electromagnetic induction, this varying flux will induce a voltage into the secondary winding.
EMF equation for 1ø transformer: –
EMF equation for 1ø transformer: –
When a sinusoidal voltage is applied to the primary winding of a transformer, alternating flux ϕm sets up in the
iron core of the transformer. This sinusoidal flux links with both primary and secondary winding. The function
of flux is a sine function. The rate of change of flux with respect to time is derived mathematically.
The derivation of EMF Equation of the transformer is shown below. Let
- ϕm be the maximum value of flux in Weber
- f be the supply frequency in Hz
- N1 is the number of turns in the primary winding
- N2 is the number of turns in the secondary winding
- Φ is the flux per turn in Weber
As shown in the above figure that the flux changes from + ϕm to – ϕm in half a cycle of 1/2f seconds.
By Faraday’s Law
Let E1 is the emf induced in the primary winding
- Φ is the flux per turn in Weber
E = -N dΦ/dt
Types of Single-Phase Transformers
Single-phase transformers are classified based on their construction, functionality, and application requirements. Each type possesses unique characteristics that make it suitable for specific electrical scenarios. Below is a comprehensive examination of the various transformer types with their technical specifications.
Core-Type Transformers
The core-type transformer features a rectangular magnetic core with windings placed on two vertical limbs. This design provides better natural cooling due to increased surface area exposure. The windings are typically arranged concentrically, with low-voltage windings placed closer to the core to reduce insulation requirements. Core-type transformers are predominantly used in high-voltage applications up to 33kV due to their superior magnetic circuit characteristics.
Shell-Type Transformers
In shell-type construction, the windings are completely surrounded by the core, creating a protective “shell” configuration. This design offers better mechanical support and reduced leakage flux, making it ideal for low-voltage, high-current applications. The interleaved winding arrangement provides improved short-circuit withstand capability, with typical applications including welding transformers and furnace transformers.
Step-Up Transformers
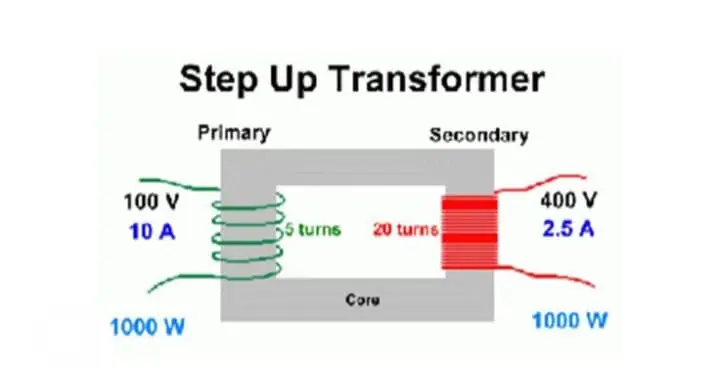
Step-up transformers increase voltage from primary to secondary windings through a turns ratio greater than 1. These transformers feature specialized insulation systems to handle elevated voltages.
Classification by Voltage Transformation
Single-phase transformers are primarily categorized based on their voltage conversion capability. Step-up transformers increase voltage from primary to secondary windings, making them essential for power transmission systems where higher voltages reduce line losses. These typically have fewer turns in the primary winding compared to the secondary. Conversely, step-down transformers decrease voltage levels, featuring more turns in the primary winding than the secondary, and are ubiquitous in residential and commercial power distribution networks where safe voltage levels are required for end-use equipment.
Isolation Transformers
Isolation transformers maintain a 1:1 turns ratio while providing complete electrical separation between primary and secondary circuits. These specialized units serve critical functions in sensitive electronic equipment by preventing ground loops and suppressing electrical noise. Medical-grade isolation transformers incorporate enhanced insulation systems for patient-connected equipment, while industrial versions protect control circuits from power line disturbances. The isolation capability also improves safety by eliminating direct conductive paths between input and output.
Autotransformers
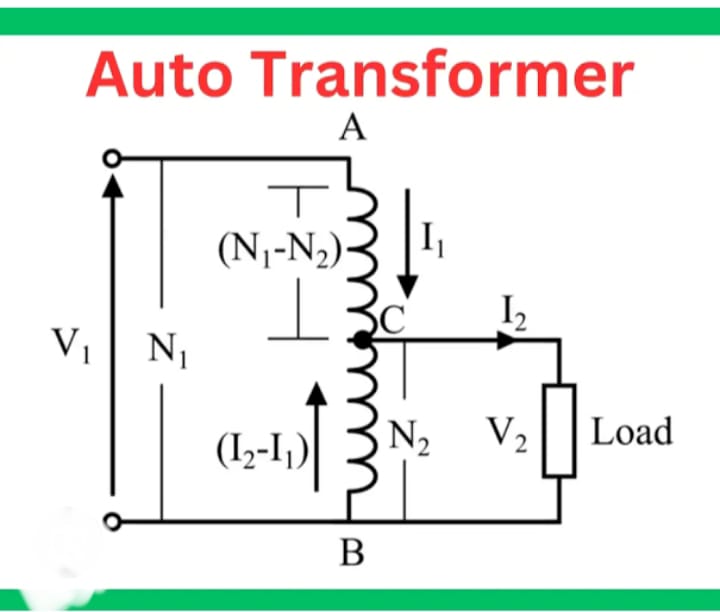
Autotransformers employ a single winding with multiple taps to achieve voltage transformation, unlike conventional two-winding designs. This configuration offers advantages in size, weight, and cost efficiency, particularly for moderate voltage ratio applications. The shared winding portion carries the difference between primary and secondary currents, resulting in reduced material requirements. However, the absence of electrical isolation between input and output limits their use in applications requiring complete circuit separation. Variable autotransformers (Variacs) incorporate a sliding contact to provide continuously adjustable output voltage.
Instrument Transformers
Two specialized types serve measurement and protection functions in power systems. Potential transformers (PTs) precisely step down high voltages to standardized low levels (typically 120V) for metering and relay circuits, maintaining accurate voltage ratio and phase relationship. Current transformers (CTs) proportionally reduce high currents to standardized values (usually 5A or 1A) while isolating measurement equipment from high-voltage lines. Both types feature enhanced accuracy characteristics and are designed to maintain performance within specified burden limits.
High-Frequency Transformers
Operating well above power line frequencies, these transformers are engineered for switching power supplies, inverters, and radio frequency applications. Their designs minimize parasitic capacitance and leakage inductance through specialized winding techniques and often employ ferrite cores to reduce high-frequency losses. The compact size and improved efficiency at elevated frequencies make them essential components in modern power electronics, though their core materials and construction differ significantly from conventional power transformers.
Resonant Transformers
These specialized units incorporate tuned circuits to operate at specific resonant frequencies, enabling applications in radio transmission, induction heating, and high-voltage testing. Tesla coils represent a well-known example, utilizing resonant coupling to achieve extremely high secondary voltages. The design carefully controls leakage inductance and distributed capacitance to establish the desired resonant characteristics, with the transformer itself forming part of the resonant circuit.
Construction of a Single-Phase Transformer
The construction of a single-phase transformer involves carefully designed components that work together to enable efficient voltage transformation. Each element plays a critical role in the transformer’s performance, efficiency, and durability. Below is a detailed breakdown of the key components and their characteristics.
Core Assembly
The transformer core serves as the magnetic pathway for flux linkage between windings. Modern transformers use laminated silicon steel cores to minimize eddy current losses. The laminations are insulated from each other with a thin varnish coating, typically 0.3-0.5mm thick, which significantly reduces circulating currents while maintaining high magnetic permeability.
Winding Configuration
Single-Phase Transformers windings consist of precisely wound copper or aluminum conductors arranged concentrically around the core. High-voltage windings use finer gauge wire with more turns, while low-voltage windings employ thicker conductors. The winding process requires careful layer insulation using materials like kraft paper or Nomex to prevent inter-turn shorts and withstand operational voltages.
Insulation System
A multi-layer insulation approach protects the Single-Phase transformer from electrical breakdown. Major insulation components include:
- Conductor insulation (enamel or paper wrap)
- Layer insulation between winding sections
- Main insulation between windings and core
- Barrier insulation between primary and secondary windings
Cooling Mechanism
Cooling systems vary by transformer type and application:
Cooling Type | Description | Application | Efficiency |
---|---|---|---|
Oil-Immersed | Mineral oil circulates through windings | Power distribution | 98-99% |
Dry-Type | Air-cooled with ventilation channels | Indoor installations | 95-97% |
Cast Resin | Epoxy-encapsulated windings | Harsh environments | 96-98% |
Terminal Arrangement
Bushings and terminals provide secure external connections while maintaining proper insulation. High-voltage transformers use porcelain or polymer bushings rated for the system voltage, with careful attention to creepage distance based on environmental conditions. Terminal arrangements follow standardized marking (H1-H2 for primary, X1-X2 for secondary) to ensure proper phasing.
Enclosure and Protection
The Single-Phase transformer housing provides mechanical protection and environmental sealing. Outdoor units feature weatherproof enclosures with corrosion-resistant coatings, while indoor units may include sound-dampening materials. Modern designs incorporate pressure relief devices, temperature sensors, and moisture indicators for operational safety.
Efficiency and Losses in Single-Phase Transformers
Transformers are remarkably efficient electrical devices, typically achieving 95-99% efficiency in power conversion. However, like all electromagnetic systems, they experience inherent energy losses that affect their performance. These losses primarily occur in the core and windings, with additional minor losses from other factors.
Core Losses (Iron Losses)
Core losses remain constant regardless of load and consist of two main components:
Hysteresis Loss
This results from the repeated magnetization and demagnetization of the core material during each AC cycle. The energy required to realign magnetic domains in the silicon steel core converts to heat. Using grain-oriented electrical steel with specially treated crystalline structures significantly reduces these losses.
Eddy Current Loss
Induced circulating currents within the core material generate this loss. Transformer manufacturers minimize it through laminated core construction, where thin steel sheets (0.3-0.5mm thick) are insulated from each other. The laminations effectively break up potential current paths while maintaining excellent magnetic properties.
Copper Losses (I²R Losses)
These variable losses depend on the load current and occur in the transformer windings:
Primary Winding Loss
The resistance of primary winding copper conductors causes power dissipation proportional to the square of the primary current (I₁²R₁).
Secondary Winding Loss
Similarly, the secondary winding exhibits resistance-related losses based on secondary current (I₂²R₂). Using larger conductor sizes reduces these losses but increases transformer size and cost.
Stray and Dielectric Losses
Additional minor losses include:
Stray Flux Losses
Leakage flux induces small eddy currents in nearby metallic parts like the transformer tank or clamping structures.
Dielectric Losses
The insulating materials between windings and to ground experience small but measurable losses, especially in high-voltage transformers.
Loss Comparison Table
Loss Type | Cause | Reduction Method | Typical % of Total Loss |
---|---|---|---|
Hysteresis | Magnetic domain realignment | Grain-oriented silicon steel | 30-40% |
Eddy Current | Circulating core currents | Laminated core construction | 20-30% |
Copper (Primary) | Primary winding resistance | Optimized conductor sizing | 15-25% |
Copper (Secondary) | Secondary winding resistance | Proper winding design | 15-25% |
Stray Losses | Leakage flux | Careful magnetic circuit design | 2-5% |
Dielectric | Insulation polarization | High-quality insulating materials | 1-3% |
Factors Affecting Efficiency
- Load Level – Transformers reach maximum efficiency at 70-80% of full load
- Power Factor – Lower power factors increase effective losses
- Operating Temperature – Higher temperatures increase conductor resistance
- Frequency – Core losses increase with frequency
- Core Material – Advanced amorphous metals reduce hysteresis losses
Applications of Single-Phase Transformers
Single-phase transformers serve as indispensable components across numerous electrical applications, providing voltage transformation, isolation, and power distribution capabilities. Their versatility makes them essential in both everyday devices and specialized industrial equipment.
Application | Transformer Type | Purpose |
---|---|---|
Power Distribution | Step-Up/Step-Down | Voltage regulation |
Household Appliances | Step-Down | Safe voltage for devices |
Industrial Machines | Isolation | Noise reduction |
Electronic Devices | Autotransformer | Voltage conversion |
Conclusion
Single-phase transformers are indispensable in modern electrical systems, enabling efficient power distribution and voltage conversion. Understanding their construction, working principles, and applications is essential for engineers, technicians, and enthusiasts alike.